"I'm Building a Rocket Engine That Could Reach Alpha Centauri": Princeton Satellite Systems President Michael Paluszek on Fusion Propulsion & the Future of Space Exploration
Princeton Satellite Systems founder Michael Paluszek discusses fusion propulsion, space exploration, and the future of interstellar travel with groundbreaking technology that could one day reach Alpha Centauri.
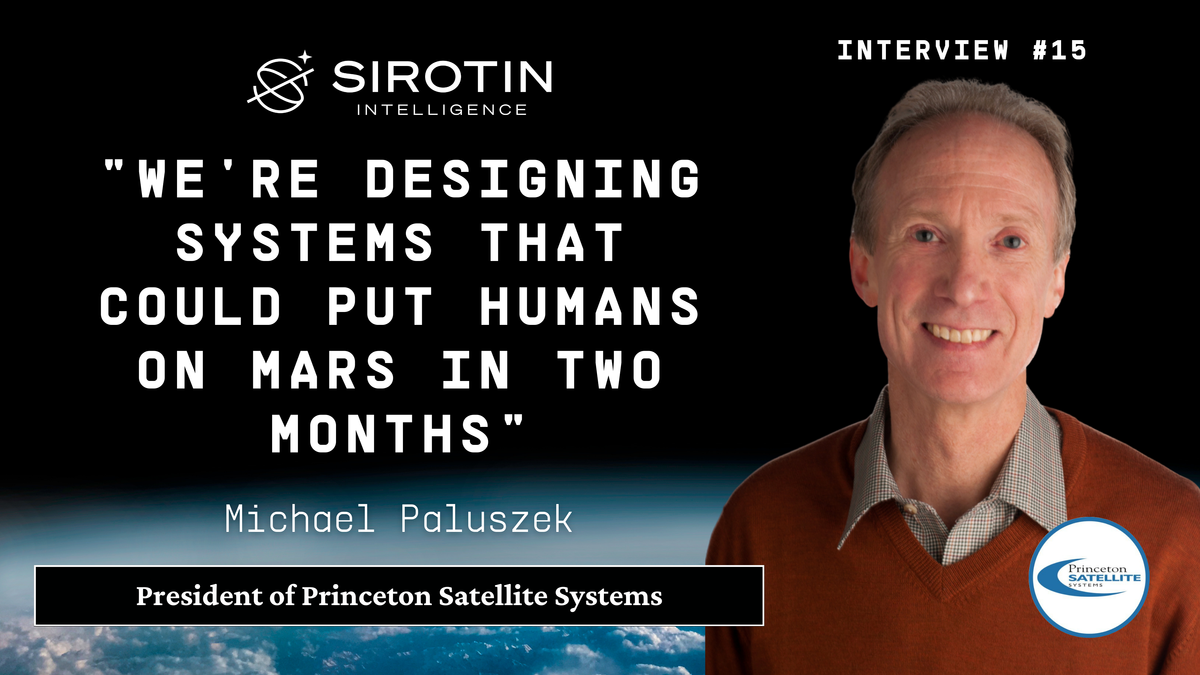
The Soviet radio crackled with news of Apollo 11's moon landing as a young American high school student stood transfixed in the summer of 1969. While Cold War tensions defined the geopolitical landscape, Michael Paluszek witnessed firsthand how space exploration transcended political boundaries when Soviet citizens approached his friends to offer congratulations. That moment—simultaneously personal and historic—would anchor Paluszek's lifelong fascination with the final frontier and launch a career that would span from early Space Shuttle control systems to the development of the Mars Observer delta-V control system and the current Mars sample return ascent stage.
Now, as President of Princeton Satellite Systems, Paluszek stands at the frontier of space propulsion with Starfire—a fusion propulsion concept developed with Princeton Plasma Physics Laboratory that could reduce travel time to Pluto from nine years to just four. Unlike conventional fusion approaches, Paluszek's system produces minimal neutron radiation, making it ideal for spacecraft, and could generate enough electrical power to revolutionize deep space missions. In an era dominated by billionaire-funded ventures, Paluszek represents a different tradition: the methodical engineer pushing the boundaries of what's possible through physics and mathematics, working to collapse interplanetary travel times from years to months, from months to days—and perhaps someday, to take humanity to the stars.
What first sparked your fascination in space?
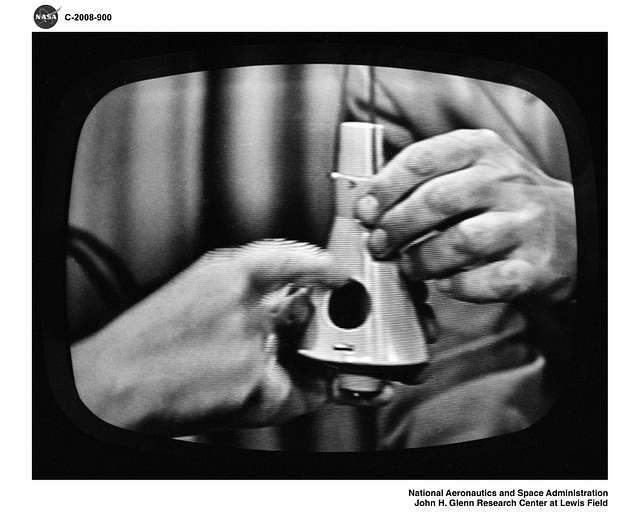
I first became interested in space in the 1950s, during the early days of satellite launches. The Mercury program, in particular, was incredibly exciting and captured my attention. That initial interest deepened with the Gemini and Apollo programs, which were at the cutting edge of technology at the time. Astronauts and their missions were constantly in the news, and space exploration was advancing rapidly.
One of the biggest milestones that fueled my passion was the Apollo moon landings. Around the same time, the movie 2001: A Space Odyssey was released. While the film included some fantastical elements, all the spacecraft and technology were designed by aerospace engineers to be as realistic as possible. Of course, we didn’t send astronauts to Jupiter in 2001, but the technology depicted in the film was considered plausible for that time frame. This further cemented my interest in space exploration.
A unique experience that stands out was being in the Soviet Union during the Apollo 11 moon landing. I had traveled there on a summer trip after my freshman year of high school, thinking I would be back before the launch—only to find out that they stuck to schedule. It was a fascinating moment. Some of my friends shared how Soviet citizens would approach them to congratulate them on the landing. It was a reminder of how space exploration, even amid political tensions, had the power to bring people together. That international spirit of space programs and technological collaboration continues to excite me today—now more than ever, as space exploration remains a global effort.
You're collaborating with Princeton Plasma Physics Laboratory on nuclear fusion propulsion. How does your work on the Princeton Field-Reversed Configuration concept potentially transform space travel capabilities?
We call it Starfire—a much more exciting name than the acronym. The technology is based on the Princeton Field-Reversed Configuration (PFRC), which was invented by Dr. Samuel Cohen at the Princeton Plasma Physics Laboratory (PPPL). One of its key features is that it uses deuterium and helium-3 as fuel, which offers several advantages over traditional fusion approaches.
To provide some fusion basics: fusion occurs when two atoms collide and convert a small portion of their mass into energy. Many researchers worldwide are working to harness this process. One of the largest projects is ITER, currently being built in France, which I had the chance to visit with my family—an incredibly exciting experience. In the late 1990s, the Tokamak Fusion Test Reactor (TFTR) successfully burned deuterium and tritium as fuel, demonstrating that plasma fusion was possible, though it didn’t achieve net energy gain. That was a groundbreaking moment. The European Joint European Torus (JET) has also made significant strides in fusion research.
To achieve fusion, the fuel must be heated to extremely high temperatures. Instead of using Kelvin, I’ll refer to kilo-electron volts (keV) since they are a more convenient unit—approximately a 10,000-to-1 ratio compared to degrees Kelvin (or Celsius). The first practical fusion reaction—deuterium-tritium (DT)—occurs at around 5 keV, which is why it has been the primary focus of most fusion research. However, the PFRC technology we’re developing operates at much higher temperatures, needing to reach around 100 keV. This is not unrealistic; TFTR previously achieved approximately 40 keV, making this goal attainable.

One of the key advantages of using deuterium-helium-3 is that nearly all the energy produced remains in charged particles rather than high-energy neutrons. By contrast, DT fusion releases most of its energy in the form of neutrons, which can severely damage reactor structures. Developing materials that can withstand that damage is a major challenge. Because our system minimizes neutron production, it is much better suited for space applications—ensuring longer-lasting reactors.
We do have side reactions, such as deuterium combining with itself to produce some tritium and neutrons. However, our design accounts for this by keeping the system compact—approximately the right size for a rocket. This configuration allows tritium to exit before it has a chance to fuse, reducing the neutron damage problem.
Our heating system is another distinguishing feature. It uses radio frequency (RF) waves, similar to an induction motor, to both confine the plasma and drive the current to heat it. This is a much simpler approach than other fusion machines, which often require multiple complex heating methods, such as neutral beams or self-heating from fusion products. In contrast, our system is a driven machine, meaning we actively sustain the plasma rather than relying on self-heating.
To generate thrust, we introduce additional ionized hydrogen, which mixes with the high-energy alpha particles produced by fusion. This enables us to achieve a reasonable amount of thrust—around 5 to 10 Newtons. While this is far less than the enormous thrust produced by chemical rockets at launch, our system operates at extremely high exhaust velocities. According to fundamental rocket theory, the higher the exhaust velocity, the less fuel is required to achieve a given velocity change. This translates into significant advantages for space travel.
For example, a mission to Pluto that took NASA’s New Horizons nine years using conventional chemical propulsion and gravity assists could be completed in four years using Starfire. This mission would put the spacecraft in Pluto orbit, instead of just flying by Pluto. Additionally, this technology allows for much greater flexibility in launch windows since missions wouldn’t be as dependent on planetary alignments for gravity assists.
Another major benefit is that, because Starfire is a fusion reactor, it also generates a significant amount of electrical power. This could revolutionize space exploration by enabling powerful communication systems and advanced scientific instruments. A great example is NASA’s proposed Jupiter Icy Moons Orbiter mission, which planned to use a fission reactor to generate 100 kilowatts of electrical power.
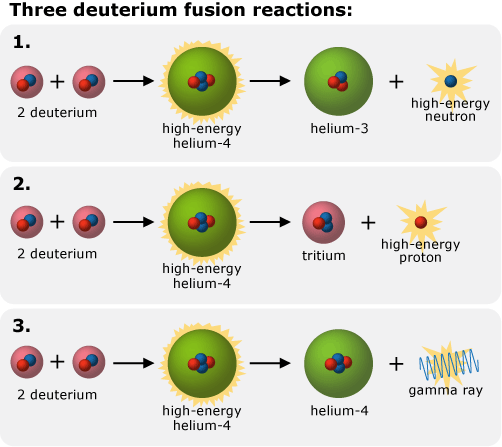
This would have allowed for 25 kilowatts of power dedicated purely to scientific experiments. In contrast, most current deep-space missions operate on about 100 watts—meaning that future spacecraft powered by Starfire could perform vastly more complex and data-intensive scientific studies.
That said, we still have critical milestones ahead. The most recent prototype, PFRC-2, built at PPPL, conducted valuable experiments, but it has yet to reach the temperatures necessary to fully validate the physics of our approach. Our next step is to construct a larger machine, which will cost around $10 million, capable of reaching fusion-relevant conditions—about 5 keV. This will allow us to confirm whether the plasma remains stable and contained long enough for effective fusion to occur.
The good news is that the core technology already exists. Our system is fundamentally similar to an MRI machine (in terms of magnetic fields) combined with a gas turbine engine. Unlike DT-based reactors, we don’t require exotic materials because our system avoids issues with extreme neutron flux. However, as with any major engineering challenge, it’s best to take an incremental approach rather than immediately building a full-scale propulsion system and spacecraft.
A great example of this method is Commonwealth Fusion Systems, a leading company in commercial fusion. They are currently developing SPARC, a smaller version of what they hope will eventually become ARC, their full-scale power reactor. Our plan follows a similar pathway—proving the physics with a mid-scale prototype before scaling up to revolutionize space propulsion.
Having led both the Mars Observer delta-V control system and now working on Mars sample return ascent stage - how has Mars mission design evolved in your experience?
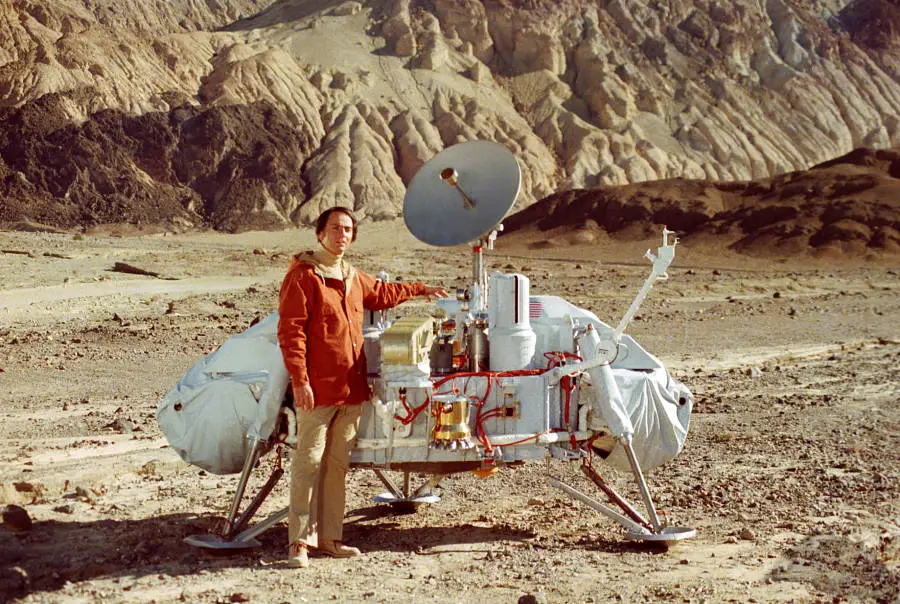
Mars mission design has evolved significantly over the years. If we go back to the 1970s, Viking was the first spacecraft to land on Mars. It was an incredibly challenging mission—especially considering that just a decade earlier, we had only begun landing robotic spacecraft on the Moon with Surveyor.
Since then, missions have become far more complex. The Viking landers were stationary and carried scientific instruments to analyze the Martian surface. In contrast, today’s missions feature rovers that can traverse vast distances across the terrain. We even have helicopters, like Ingenuity, which demonstrate powered flight on another planet—an incredible technological achievement. And that’s just on the robotic side.
The next major leap will be human exploration, which will require a host of new technologies. One of the biggest challenges is getting astronauts to Mars quickly to minimize their exposure to cosmic radiation and the psychological strain of long-duration spaceflight. Our Starfire fusion propulsion concept could make a huge impact here, potentially reducing travel time to Mars to just 60 days—far shorter than conventional chemical propulsion, which takes many months.
Another key requirement for human missions is surface infrastructure. Astronauts will likely need to live underground to shield themselves from radiation, which means we will need autonomous robotic excavation equipment to prepare habitats in advance. Ideally, we would establish a functioning Mars base before humans even arrive, ensuring that the environment is safe and sustainable.
A major challenge we are currently working on is designing ascent vehicles capable of launching from the Martian surface. While we’ve launched small payloads from the Moon and even asteroids, launching a spacecraft from Mars introduces additional complexities due to the planet’s stronger gravity and thin atmosphere.
One of the most exciting aspects of the Mars Sample Return mission is that it involves multiple spacecraft working together. The ascent vehicle must launch samples from Mars and rendezvous with an orbiter, which will then return them to Earth. This level of precision is unprecedented for interplanetary missions. The Earth Return Orbiter, which is being developed by the European Space Agency, is arguably one of the most advanced spacecraft ever proposed.
Ultimately, as we push for more ambitious science and human exploration, we must continue to develop new technologies. There is always something new to solve in planetary exploration—no mission is ever routine.
Your work spans from early Space Shuttle control systems to modern CubeSats. What key developments in attitude control systems have enabled the current small satellite revolution?

The CubeSat revolution started as a student project—an idea by some faculty members who thought it would be fun for students to build small satellites for hands-on learning.
What began as an educational tool quickly evolved into an entire industry, as people realized these small satellites could have practical applications.
One of the biggest changes CubeSats have driven is the development of low-cost instruments, including star cameras and reaction wheels. Traditional systems, like those built by Honeywell, are designed to last 15 years and withstand the harsh conditions of space, making them extremely sophisticated but also very expensive. The CubeSat movement introduced a different philosophy: build simpler, lower-cost systems that may not last as long but allow for greater experimentation and accessibility.
When I was at GE Astro Space, designing an attitude control system was a highly specialized skill—only about a dozen people in the world had expertise in it. Today, thousands of students and engineers have worked on CubeSat attitude control systems. Because these satellites don’t require the same level of radiation hardening as large, long-duration spacecraft, they can be built more affordably. This has dramatically lowered the barriers to entry, allowing more people to develop and refine spacecraft technologies.
This expansion of knowledge has led to rapid technological advancements. The more people who work in an industry, the faster innovation occurs. In the early days, getting a star camera onto a geostationary spacecraft was a major challenge due to cost and performance limitations. Now, thanks to advancements in processing power, star cameras have proliferated, making it much easier to build high-performance spacecraft.
The real revolution has been the shift toward low-cost, iterative design. Instead of relying solely on expensive, long-duration missions, we now see a growing ecosystem of small, rapidly deployable satellites. This democratization of space technology is accelerating the pace of innovation and enabling entirely new mission concepts that wouldn’t have been feasible just a few decades ago.
Could you elaborate on your current two-stage horizontal takeoff launch vehicle project using hydrogen-fueled ramjet? What advantages does this approach offer?
Our concept involves developing a two-stage, fully reusable launch vehicle that takes off horizontally like an aircraft. Here’s how the system works in detail:
- The vehicle begins its journey on a conventional runway, taking off with standard turbofan engines.
- As it climbs and accelerates, it transitions to a hydrogen-fueled ramjet, which propels it to a high altitude and speeds of Mach 6 or 7.
- At that point, the second stage separates and ignites its RL-10 engine to reach orbit.
- The first stage, having completed its role, returns to the airfield using its turbofan engines for a controlled landing.
- Meanwhile, the upper stage delivers the payload, arrives at its destination, and then returns as a glider for reusability.
One of the most significant advantages of this system is that it uses atmospheric oxygen as an oxidizer for the first stage, drastically reducing the amount of onboard fuel required. This allows for a much smaller and more efficient vehicle. Additionally, because the system takes off like an aircraft, it is not restricted to traditional launch pads and could theoretically operate from multiple locations. That said, while it offers greater flexibility, it is unlikely that major commercial airports would welcome an orbital glider landing in their air traffic zones—so specialized landing sites would still be necessary.
A common question is how this system compares to larger vertical launch vehicles, such as those being developed by SpaceX. The key lies in the business model. Historically, space launch markets were built around geostationary communications satellites, which required large, powerful rockets. In fact, the Germans previously designed a vehicle similar to our two-stage horizontal launch system, but it was significantly larger because the only viable market at the time was placing large communications satellites (COMSATs) into orbit.

However, the commercial space landscape is evolving. In recent years, researchers aboard the International Space Station (ISS) have been developing pharmaceuticals and semiconductor materials, and a surprising discovery has emerged: some drugs are much easier to manufacture in microgravity than on Earth. This is particularly true for certain cancer treatments, where gravity disrupts the precise formation of molecular structures. Semiconductor materials also benefit from space-based manufacturing due to the pristine vacuum environment.
Now, imagine a scenario where a pharmaceutical company requires a specialized drug that can only be synthesized in orbit. A doctor might say, “I need this drug in 48 hours,” but under the current spaceflight model, waiting for a traditional rocket launch is not practical. This is where our system could revolutionize space access. Instead of scheduling weeks or months in advance for a vertical rocket launch, a rapid-turnaround, horizontal takeoff vehicle could enable the same kind of fast-paced logistics we have on Earth today—similar to how Amazon Prime delivers goods in a single day.
Beyond pharmaceuticals, this capability would benefit semiconductor manufacturers, allowing them to send new materials into orbit, process them within a day or two, and return them to Earth just as quickly. The entire business model hinges on the existence of a strong in-orbit manufacturing economy, but if such a market takes hold, this kind of rapid-response spaceflight would become indispensable. We estimate that a vehicle capable of carrying around 500 kilograms to orbit and back would be ideal for this emerging industry. Notably, the European Space Agency is also developing a reusable vehicle with a similar payload capacity, suggesting that others recognize this as a valuable market segment.
While much of this work is still in the experimental phase aboard the ISS, if in-space manufacturing proves commercially viable, this type of launch vehicle will be a critical enabler. As an added benefit, hydrogen-fueled ramjets could also have applications beyond space travel. In the future, this technology could enable hypersonic passenger flights, reducing travel times dramatically. For example, an aircraft powered by a hydrogen-fueled ramjet could fly from Newark to Singapore in just two hours. Hydrogen, with its higher energy content compared to traditional jet fuel, makes such advancements much more feasible.
Ultimately, this project is not just about improving space access—it’s about creating an entirely new paradigm for rapid, reusable, and efficient space transportation. By bridging the gap between orbital logistics and Earth-based supply chain models, we could enable a future where access to low Earth orbit is as routine as air travel is today.
From your experience with the GSTAR III recovery using electric thrusters to your current work on Brayton Cycle heat engines - how do you see space propulsion technology evolving?
Space propulsion technology has advanced significantly over the years, and one of the most noticeable trends is the increasing reliance on electric propulsion. Early spacecraft primarily used chemical propulsion, but we are now seeing more missions incorporate electric thrusters, particularly those powered by solar panels. Missions such as Deep Space 1, BepiColombo, and SMART-1—which traveled from Earth to the Moon using electric propulsion—demonstrate this shift.
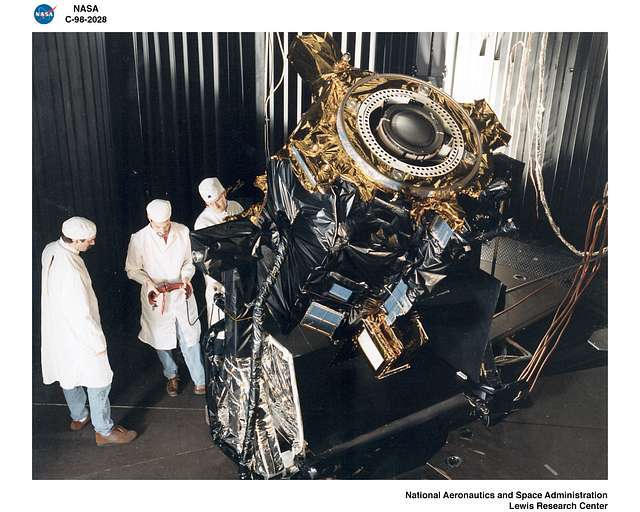
Electric propulsion offers several advantages, particularly for deep-space missions. Since electric thrusters are much more fuel-efficient than chemical rockets, they allow spacecraft to carry more scientific instruments instead of large fuel reserves. However, the effectiveness of electric propulsion depends on the power source. Most current electric propulsion systems rely on solar power, which works well up to about Jupiter’s distance from the Sun, but beyond that, solar energy becomes too weak to generate sufficient thrust.
To overcome this limitation, researchers are exploring nuclear electric propulsion. This approach was central to NASA’s proposed Jupiter Icy Moons Orbiter mission, which planned to use a fission reactor to generate electrical power for ion thrusters. In addition to enabling propulsion, the reactor would have provided 25 kilowatts of power for scientific instruments—an enormous leap compared to the roughly 100 watts available on typical deep-space probes. While the mission was ultimately canceled due to budget constraints, the concept remains highly promising for future deep-space exploration.
Another technology gaining attention is nuclear thermal propulsion. Unlike nuclear electric propulsion, which converts reactor energy into electricity to power ion thrusters, nuclear thermal propulsion directly heats hydrogen fuel, producing twice the exhaust velocity of conventional chemical rockets. This increased efficiency would significantly reduce travel times for crewed Mars missions. With chemical propulsion, a Hohmann transfer trajectory takes several months to reach Mars, but a nuclear thermal rocket could shorten the trip by several weeks, reducing radiation exposure for astronauts.
The next major step beyond nuclear propulsion is fusion-based propulsion, such as our Starfire concept. Instead of converting fusion energy into electricity and then into propulsion—an inefficient multi-step process—fusion propulsion would generate thrust directly. If successfully developed, this technology could revolutionize space travel by enabling interstellar missions. For example, a Starfire-like fusion engine could potentially reach Alpha Centauri within 300 years—still a long journey, but feasible when considering that spacecraft like Voyager have already operated for decades. Imagine placing a probe in orbit around an exoplanet in another star system—an achievement that would redefine our understanding of the universe.
One particularly exciting application of advanced propulsion is the Solar Gravitational Lens mission. If we can send a spacecraft to 650 astronomical units—650 times the distance from Earth to the Sun—it could use the Sun’s gravity as a massive lens to magnify distant exoplanets. This would allow us to observe an alien world with the same clarity as we currently see Earth from geostationary orbit. If cities exist on another planet, we would be able to detect them.
Looking ahead, the ultimate goal is to make fusion propulsion viable. If we can achieve that, we could cut the travel time to Mars down to just 60 days, significantly reducing the risks posed by space radiation and microgravity. While chemical rockets took us to the Moon and nuclear propulsion may take us to Mars, fusion propulsion will be the key to opening up the rest of the solar system—and possibly even the stars.
About Michael Paluszek
Mr. Paluszek is President of Princeton Satellite Systems, which he founded in 1992. He is designing an advanced liquid ascent stage for Mars sample return and other missions. He is also working on a two-stage horizontal takeoff launch vehicle using a hydrogen-fueled ramjet powered first stage. He was PI on the ARPA-E OPEN grant to develop a compact nuclear fusion reactor based on the Princeton Field Reversed Configuration concept. He was also PI on the ARPA-E GAMOW project to develop power electronics for the fusion industry. He was PI on a project to design a closed-loop Brayton Cycle heat engine for space applications.
Before founding PSS, he worked at GE Astro Space in East Windsor, NJ. At GE he designed or led the design of several attitude control systems including GPS IIR, Inmarsat 3, and GGS Polar platform. He also was an ACS analyst on over a dozen satellite launches, including the GSTAR III recovery. Before joining GE, he worked at the Draper Laboratory and MIT.